Recently, I received a number of questions regarding junctions. Most of the questions are related to the effect of twisted vs. parallel junctions on measurement and performance long term. To answer this question, I approached my friend and colleague at CCPI, Trevor Ford.
Below are some of the questions he answered in his reply. I hope they help you on your next project or simply answer some of the basic questions you might have while working with thermocouples.
Trevor, using your vast thermocouple sensing expertise, would you be able to provide some pros and cons of twisted (weld/no weld)/parallel welded exposed junctions?
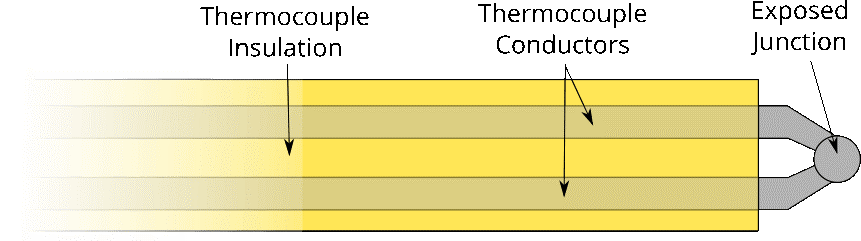
What are the issues when twisted junctions break vs. when parallel junctions break?
What’s the effect of twisting on sensitivity?
What is the right amount of twists if one must have them?
What is considered a twist? 180° or 360°?
To twist or not to twist…that is the question!
Sorry to go all Shakespeare on you.
To give everyone some preface on this, it has been common practice for many decades to twist exposed junctions, especially in lower temperature applications. I have seen other methods such as crimping, soldering, manual twisting, and the more commonplace, twist and weld junction. Over the last decade, welders who can make a nice clean and more importantly strong weld have become available. However, the question still remains with many customers as to what the right junction is. I hope that my discussion with Trevor Ford gives younger engineers who are perhaps new to thermocouples some answers.
Generally, the answer for thermocouple junctions should be a definite no twist!
The general problem with twisting thermocouple junctions is partially hinted at by some of the other questions raised. The main one is due to breaks at the weld end or to be more accurate if the junction breaks. Yes, if the weld breaks and the thermocouple weld is twisted you will get physical contact and therefore a reading. (This has come up a few times on customer visits where they experience intermittent readings.)
A junction weld break is not a major problem if you have good clean contact (tight twist) with the wires at the hot junction area and a strong enough pressure to hold the conductors together. If you do not, then you will get a reading, but it could be in error and significantly in error dependent on the contact.
Within the CCPI-Europe customer base, the temperature is high and the wires, if base metal, will become oxidized. Therefore, the chances are you will get bad contact and an incorrect reading are by an unknown factor. In this case, it is better to have an open circuit condition where you can understand the fault rather than continuing to receive potentially bad data or readings.
Therefore, under these conditions the correct number of twists is none. Parallel junctions are always a preferred choice in high temperature applications.
Even with Pt/Rh thermocouples where the wires are not going to be oxidized and should be clean, twisting is generally not looked upon as satisfactory. You may or may not get good contact and therefore potentially a good reading. Better an open circuit condition and furnace cut off than potential intermittent readings.
I can see why at low temperatures and with cleaner autoclave conditions operations with twisting have become accepted. The assessment being, “we will still get a reading even in the case of weld failure.”
The history I suspect is due to most of these composite thermocouples being made in house, at least in the early days. The quality and repeatability of the weld was an issue and many breaks occurred. This forced the creative engineers to begin twisting to and it simply stuck as the right way of doing things. The welding method CCPI-Europe and TE Wire employ are far more repeatable and reliable. The number of weld breaks we see in a year can be counted on one hand.
When you have twists, the question becomes where is the measurement taken? The answer: where the first good contact of the conductors occurs. You will get a slightly slower response time due to the increase in thermal mass the twisted weld creates. So, less twisting is preferred.
The type J AccuClave® thermocouples TE Wire & Cable manufactures may have more issues than the K due to the potential increase in oxidation from the iron conductor. However, the copper flashing should prevent that from becoming a major issue unless the end user stores the thermocouples in a humid environment (>50% relative humidity), which can expedite oxidation of iron.
If you have to twist, the number of twists should be enough to create a good electrical contact in the event of weld fracture but not too many to increase thermal mass and reduce response time. To answer whether 180° or 360° or 720° is enough, that is up to the end user.
Thanks for reading and I hope this is useful for your temperature sensing applications!
