Questions from customers who manufacture composite structures are always important to me. One big reason is because I fly over 200,000 miles a year in the very planes containing parts they supply. I’m sure you’ll agree, we want those big birds to perform flawlessly 110% of the time. My second reason is because autoclave composites manufacturing questions allow me to explain how our engineering and development team work hard at producing solutions that answer those very questions.
Over a number of years attending composite industry exhibits and my countless visits to composite production facilities around the globe, I’ve been asked a lot of interesting questions. Many people (including my marketing guy!) have suggested that I should address the most common issues with thermocouple wires used in composite cures, specifically, those thermocouple (TC) types that are used for lead/lag, parts, tools.
So here is the first installment.
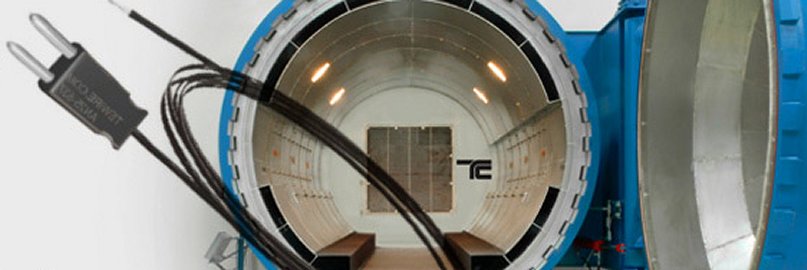
Composite cure ailment #1: Erratic temperature readings
If I had a nickel for every time someone mentioned this, I could afford a lifetime supply of Starbucks and maybe even Guinness. The complaint is almost always the same. “As the autoclave temperature climbs, the data goes upscale and either oscillates or stays upscale until the clave cools and then the TC reading drops back to a normal reading.”
I tell them that, if I were the Doctor of Autoclave Thermocouples, I would examine both ends of the TC wire.
Most often, it is the hot junction that is the culprit. It makes sense when you think about it. The hot junction is the end in contact with the part or tool. It is where the two bare metal TC conductor ends touch. As you know, metals expand when the temperature rises. If the junction of the two wires is only twisted, because of the expansion caused by the rise in temperature, the twists can open up and lose contact as the temperature rises. Without a ‘completed circuit’, the TC has zero EMF output and the control software will eventually discard that sensor. Not good.
The Doctor’s prescription for this malady is to weld the junction wires. Here’s why.
A proper inert gas weld prevents the two conductors from separating as temperatures climb.
Some may suggest just twisting the wire together and adding more turns to your twists. Realistically, this may or may not cure the problem. However, too many twists isn’t a smart answer because it will move the temperature measurement point of the junction back from the actual junction tip, which means you are not measuring the point of tip contact, but farther back from the tip where the last twist is located.
Others may suggest that you silver solder the wires together. I don’t recommended this approach because it introduces a third metal into the TC circuit that might cause errors. And a soldered junction often has a large ball of material that can indent into the composite surface.
It is possible that the other end of the TC wire could be also suspect. This is the connector end male plug. TC plugs have internal metal parts including the screws that hold the wire in contact with the pins. These metal screws expand and contract during temperature cycles. The screws can back out, which allows the wire to lose metal to metal contact. The circuit is then ‘open’ with exactly similar lost signal issues as an open hot junction.
Some attempt to fix this issue by over-tightening the screws. Over-tightening can break the small wire under the screw. And it is still possible for the screws to back out in the repeated cycles anyway.
The Doctor’s cure for loose screws is to have no screws but to weld the wire directly to the pins. Problem solved.
In future blog installments we will discuss the cures for other autoclave ailments including:
- Reversed polarity
- Broken wires/ shorted out wires
- Vacuum leaks
- Traceability and audits
- Too low temperature rated insulation
- Stripping wire under tacky tape
By the way, this doctor makes house calls. You can send your questions to me or request an appointment any time.
Click here to receive your own doctor’s prescription and evaluation the ROI of your autoclave composites manufacturing operation.
Learn More: Four Ways to Meet Increased Demands on Aerospace Autoclave Applications
